Custom Work
Here at Ralph Baker's Shoes we have been producing orthotics in-house for customers since 1997. This venture came about at a time when no other shoe retailers were doing anything remotely similar. With comfort always at the front of our mind we were excited to offer this level of service for our customers. The simple fact is that even with plenty of OTC (over-the-counter) inserts for people to better improve their footwear experience, there are still instances where these aren't enough. Gaps to be filled, if you will. We aim to fill those gaps by offering our pedorthic services to those in need. From custom orthotics to footwear modifications and everything in between.
From the time someone has had their evaluation with one of our board certified pedorthists we can usually have their orthotics ready for pick-up in one to two weeks. This quick turnover would not be possible if it weren't for our great team of individuals working in our pedorthics lab. The production process is very involved and several hands take part in ensuring quality, precision and consistency.
Featured below are photos depicting the production process from start to finish. Along with these photos are brief descriptions stating what makes our method so unique and precise.

(Our dedicated team of professionals in our pedorthics lab)

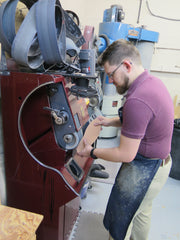
(Everette sanding plaster castings & Joseph grinding orthotics to size)
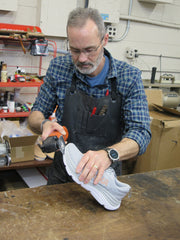
(Ralph Baker Jr. C. Ped. preparing a shoe for a custom build-up)
Production Process Described:
We create our custom orthotics by hand in our pedorthics lab. Involved in this process are several skilled hands including Joseph, Everette, Grant and of course, Ralph Baker Jr. C Ped. All things begin by molding a foot in foam to get the best impression of the foot and it's unique features. We also use a Harris Mat (ink) to collect the pressure points in the foot. Following the foam impression, plaster of Paris is mixed and poured into the foam box where the foot impression was taken. We allow several hours for the plaster to set up enough so that we can remove excess material and prep it for hardening. We typically give plaster castings 24-48 hours to harden after fine sanding. Once the plaster castings of the foot have dried and hardened they are ready to be used in the production process.
Our board certified pedorthists take many factors into consideration when hand picking materials that will be used in custom orthotics, knowing that comfort and support are paramount. For example, does the individual pronate or suponate? Do they have high or low arches? Partial amputations? Sores or bunions? What does the individual do while on their feet everyday? All of these factor into which materials are best suited for an individuals needs. Raw materials are glued and heated before being placed onto the plaster casts and into the vacuum former for precise shaping. These materials can vary from cork to EVA to Cloud posting, Spenco and much, much more. Once excess material is trimmed, the product is ready to go the grinder for a custom and finished fit as orthotics are made to fit the customer's foot and the shoe they're going to be wearing it in. We can typically have a set of custom orthotics ready within a week of the initial pedorthic evaluation.